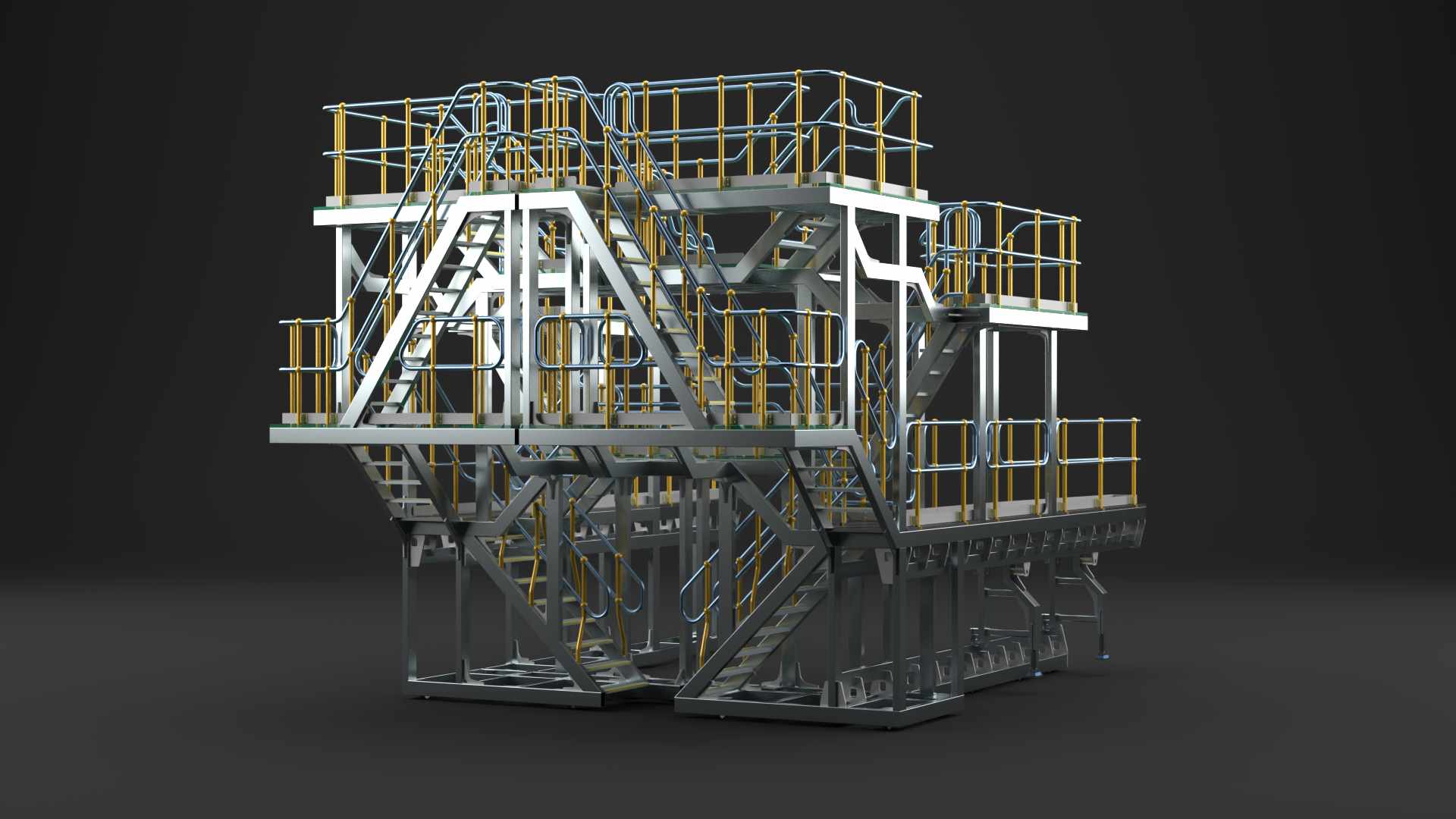
Vibration Grizzly Discharge Chute Maintenance Platform
Scope of Work
During maintenance, everything from the top-down had to be scaffold accessible. It took 12 hours and a team of four scaffolders to erect a temporary access platform and the same amount of man-hours to take it down within a shutdown period. This required an innovative design to remove an otherwise unnecessary process during stressful and time-restricted shutdown periods.
Objectives
- Cut down on the time and cost required to perform maintenance on the Vibration Grizzly Chutes.
- Create a permanent access platform for effective and safe maintenance of the machinery.
Challenges Involved
Parts of the machinery created obstructions. To combat this a sliding rail system was implemented with dollys on tracks for a fast and secure platform system.
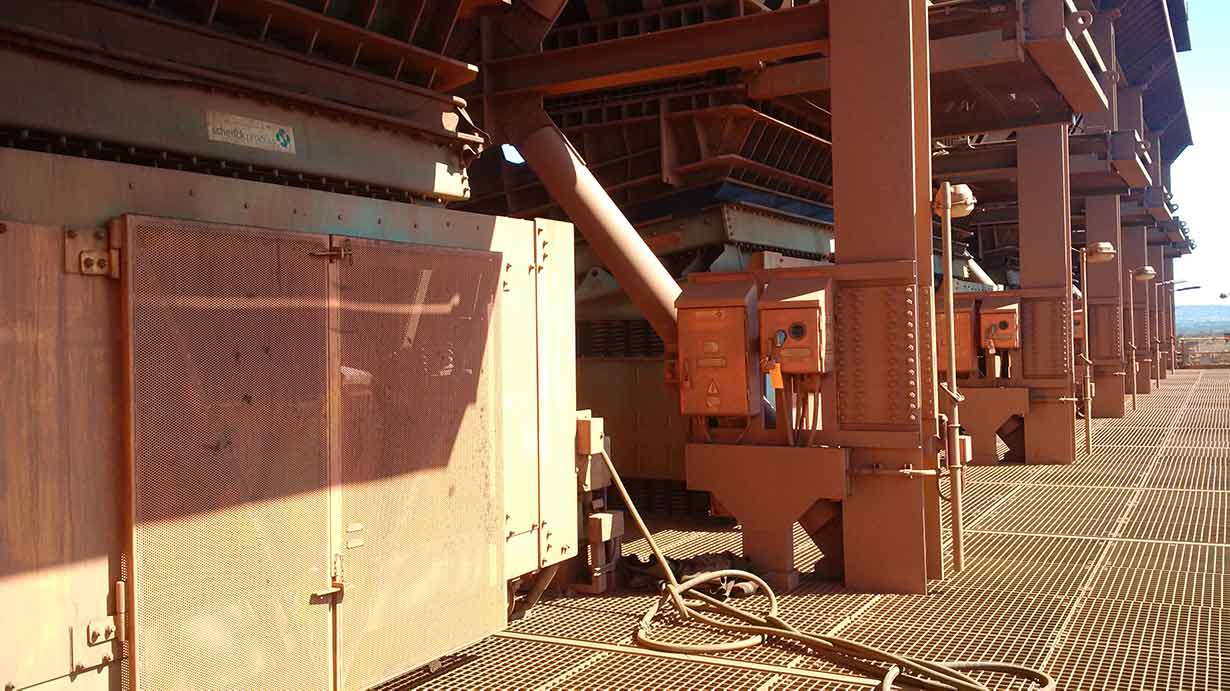
(Platform Angle 1)
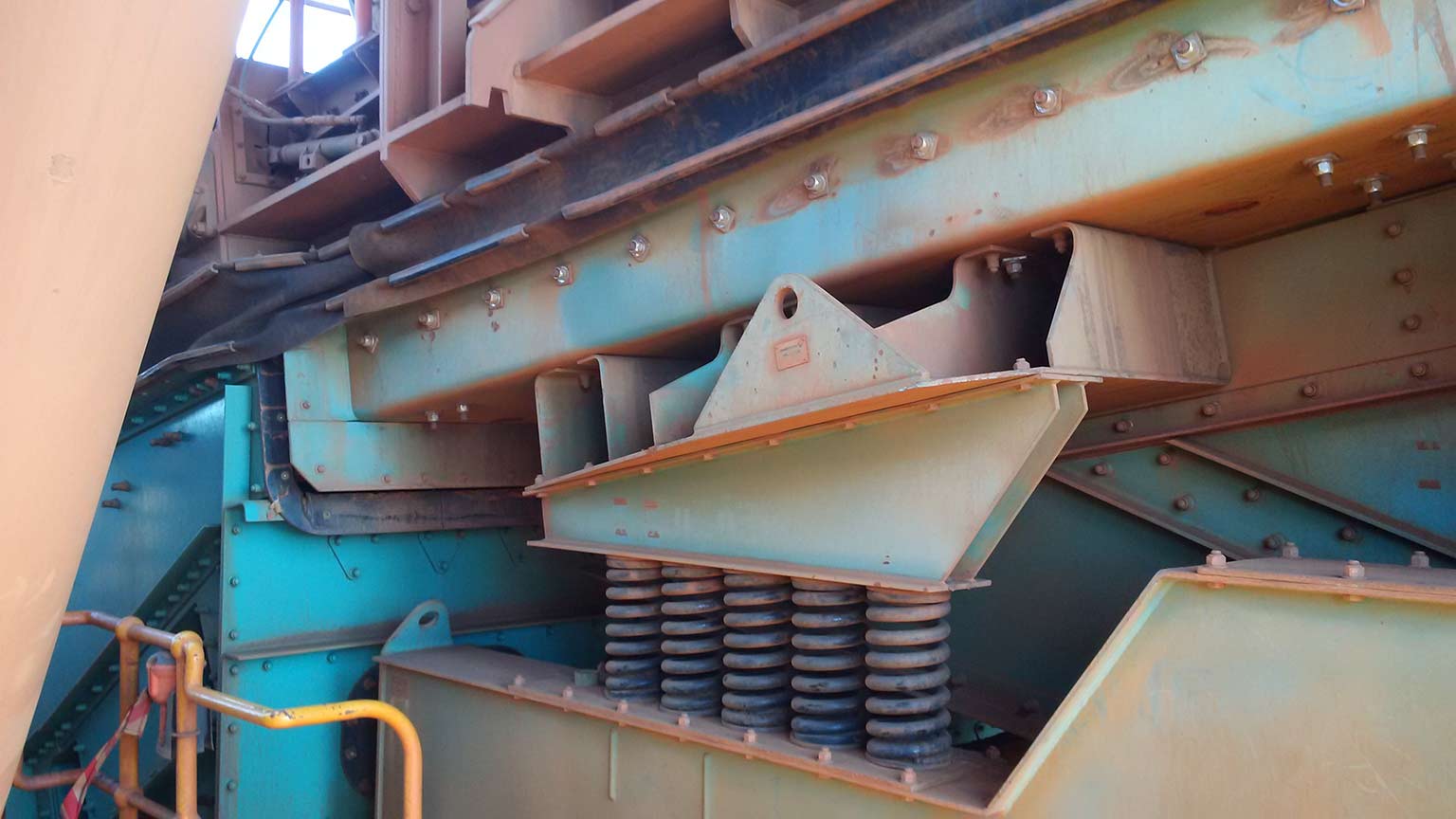
(Platform Angle 2)
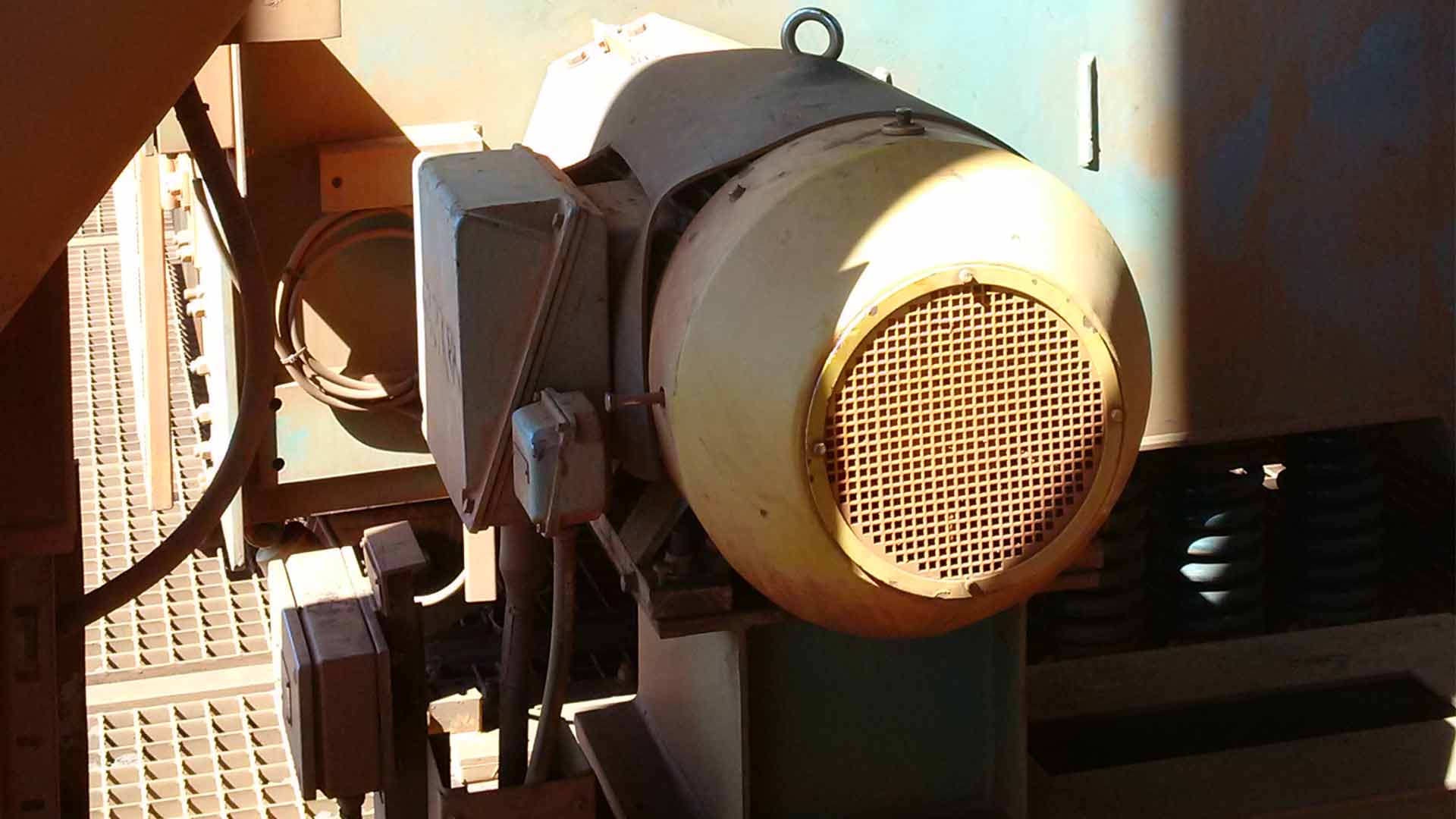
(Motor Obstruction)
Innovative Thinking
Laser scan data was used and aligned with older drafts to identify any potential errors and create an accurate reference. During the modeling process there were many considerations to account for such as: weight restrictions, accessibility, costs and complying with the Australian Safety Standards 1657:2018.
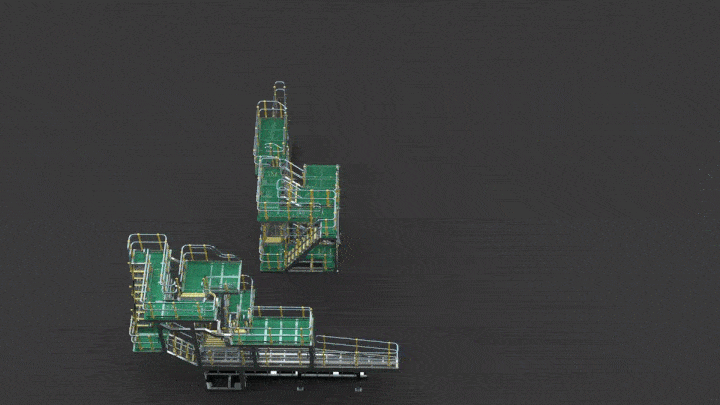
(Moving the platform via crane)

(Retractable dollys used to get around obstacles)
Accomplishments
The new design was approved and once the parts were manufactured and the structure was built it took approximately 8 weeks for the project to pay itself off.
The work access platform can be lifted up using a crane and locked into position in under less than an hour as opposed to the 24 hours it took using the previous method to prepare for maintenance.
Rio Tinto has now implemented the new design for all six of their Vibration Grizzly Discharge Chutes across the Brockman site.

(3D Viewer - Not added yet)
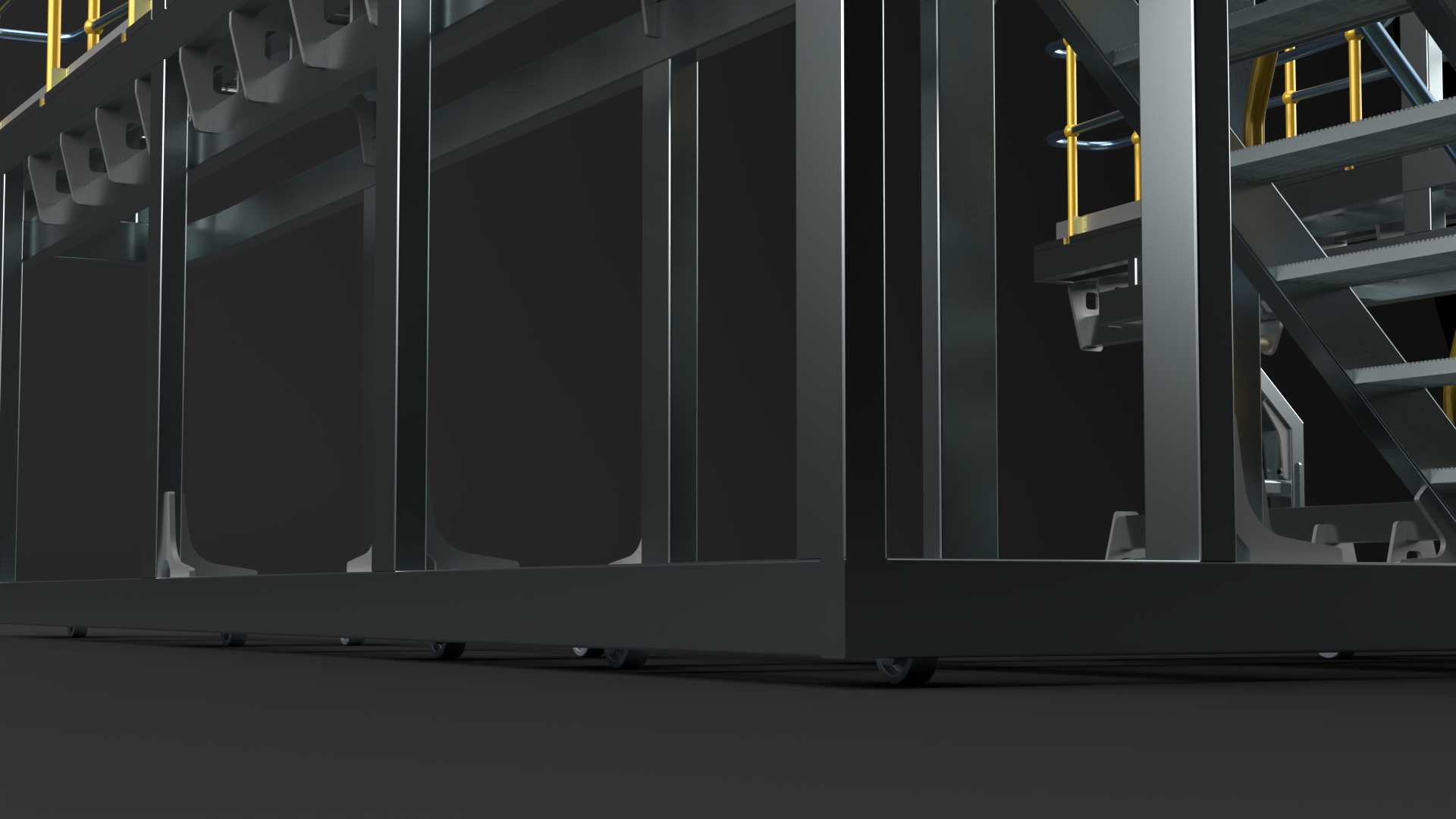
(Underneath platform)
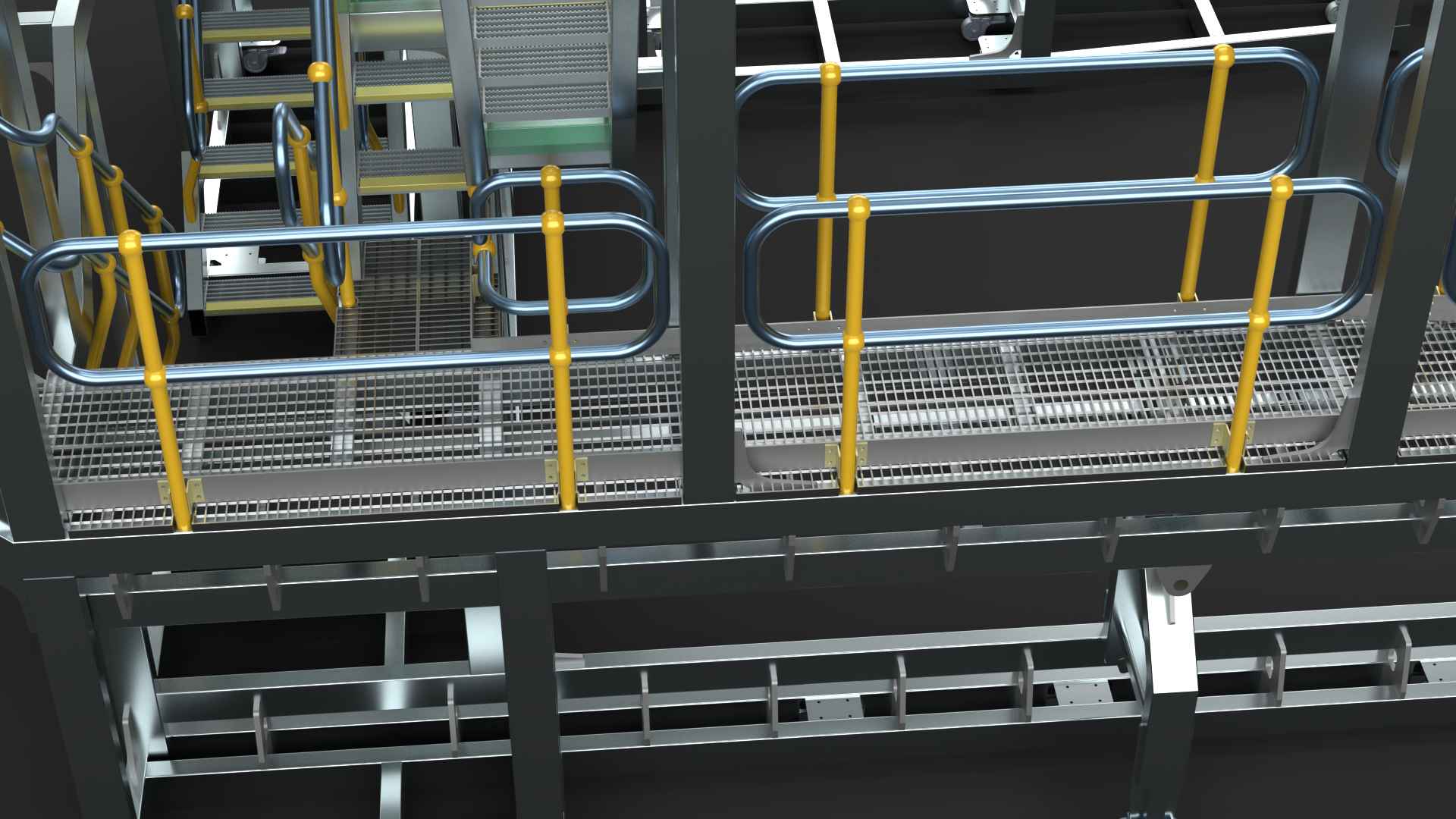
(Close up)
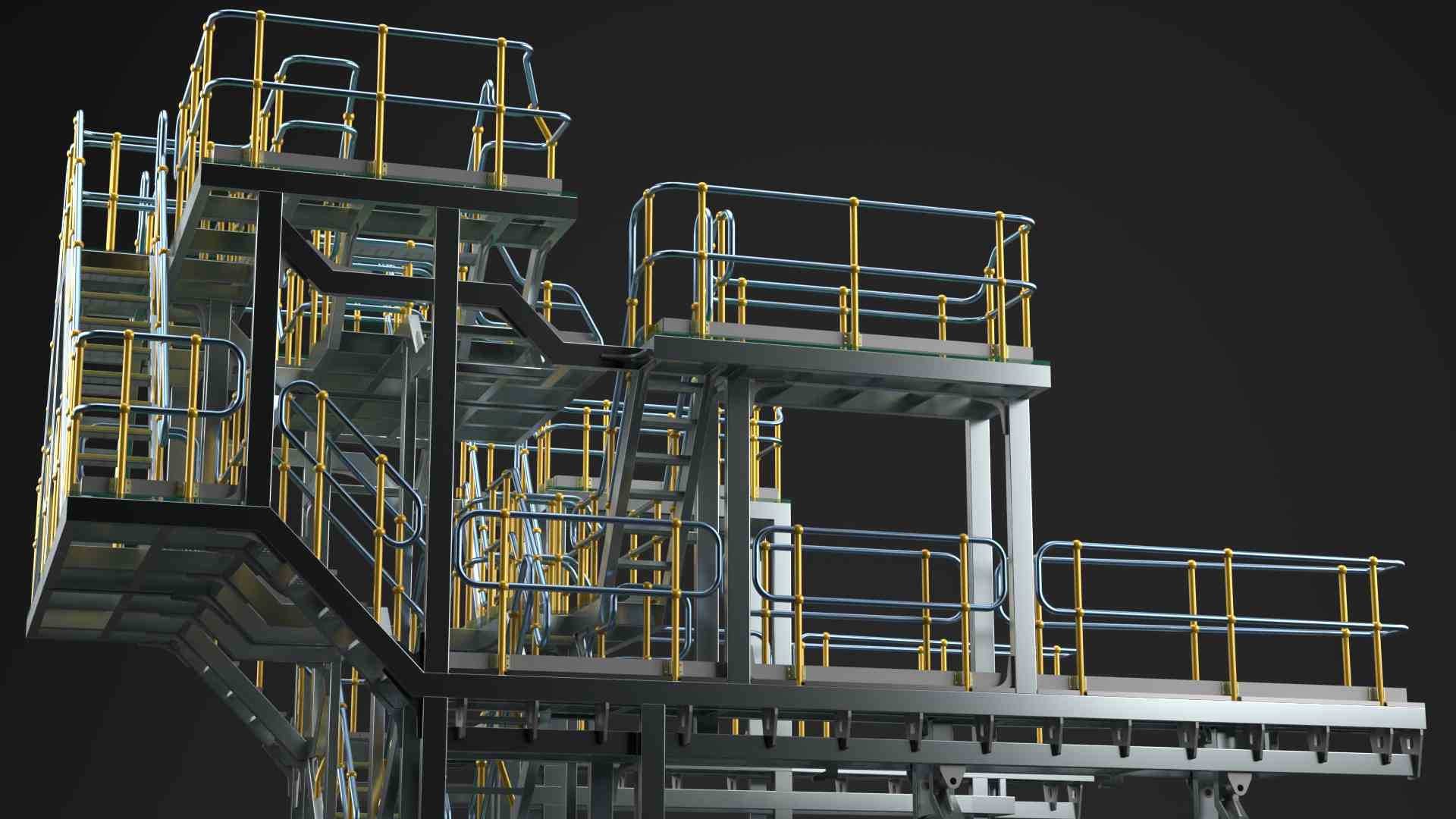
(Side view)
Other projects
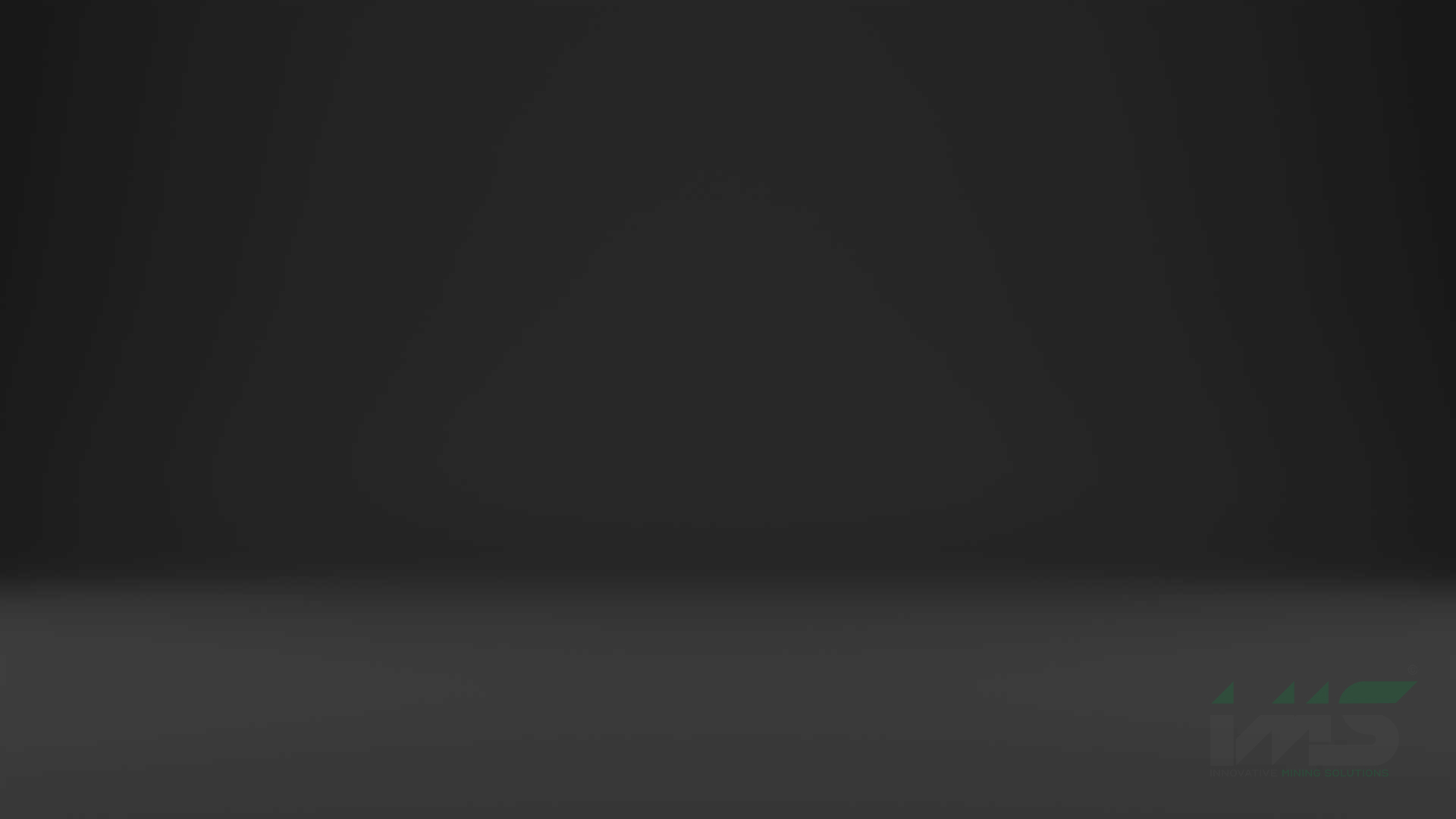
Coming Soon
...
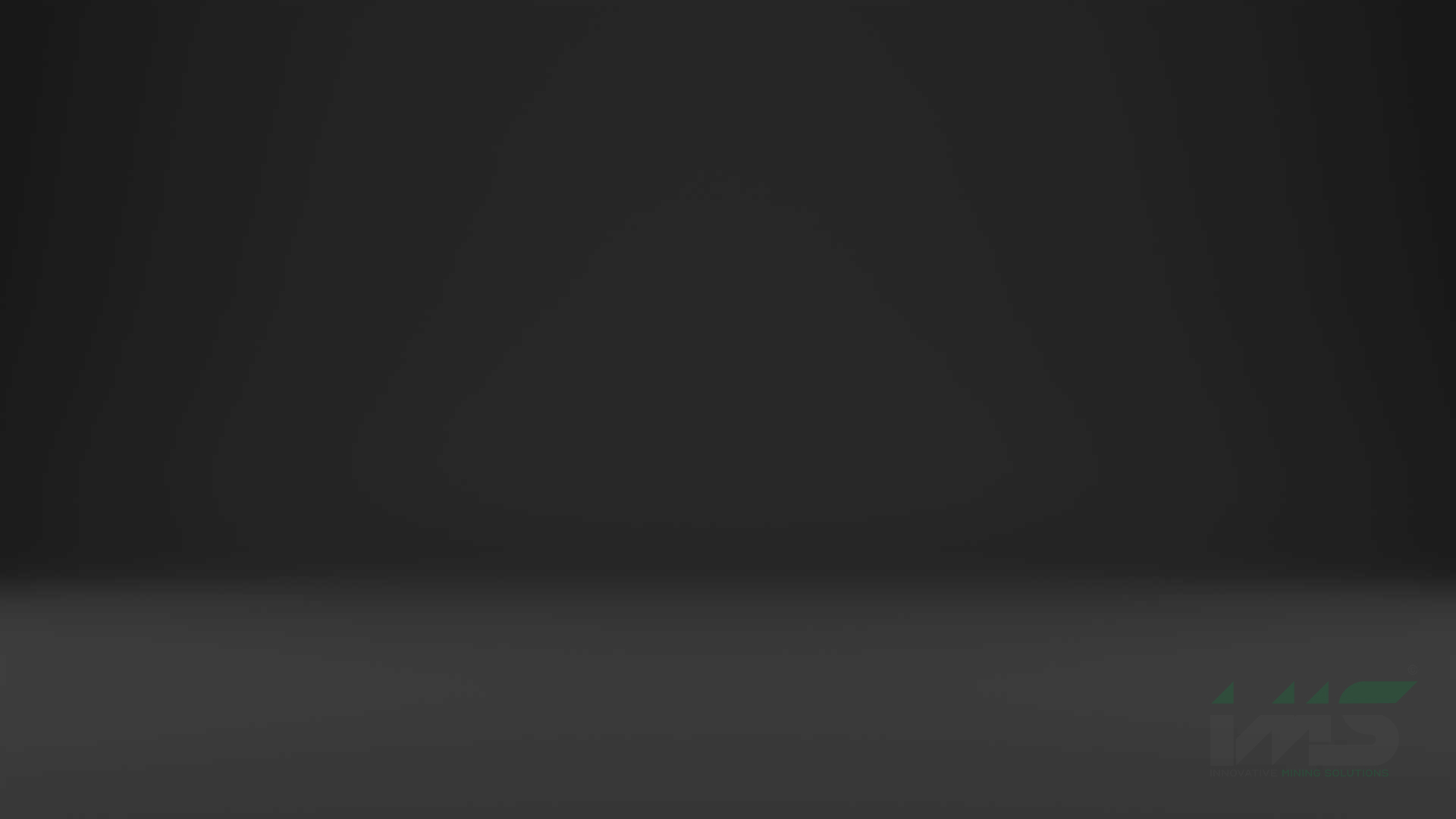
Coming Soon
...